CHOOSE ET
High Quality
Rigorously Tested
BIS Certified
Wide Variety
Standard Length:
12 meters
Option of:
5 to 20 meters
Diameter:
8 mm. to
40 mm.
Certificate:
BIS IS 13620: 1993
EPOXY-COATING
Available for all Grades of ET TMT Bars
ET Epoxy-Coated CRS TMT Bars
Fe 500, Fe 500 D, Fe 550, Fe 550 D
ET Epoxy-Coated Refined Steel TMT Bars
Fe 500, Fe 500 D, Fe 550, Fe 550 D
ET Epoxy-Coated Superior Quality Steel TMT Bars
Fe 500
All ET Epoxy-Coated TMT bar grades are available in pre-fabricated cut & bend format.
Learn more about Properties
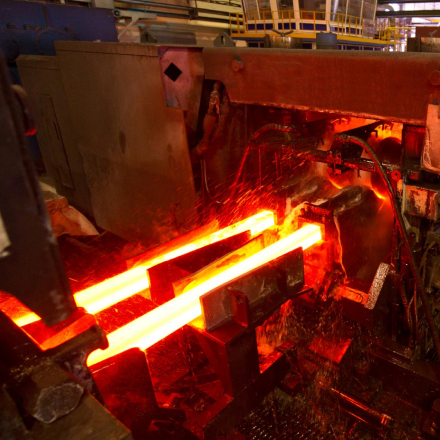
MADE TO PERFECTION
Manufacturing Process Highlights

Surface Preparation
Bars are cleaned and readied to deliver industrial-grade clean and rough surface.

Pre-heating
Induction heating is done with a high-frequency alternating current and a magnetic field at 225℃ to 245℃ .

Epoxy powder application
Heated bars are passed through a coating booth with electrically charged FBE powder cloud. Coating is done from top & bottom with the help of multiple spray guns. The heated bars help the epoxy-powder molecules form cross-linked polymers which fuse on to it in a gel form. The gel becomes an integral part of TMT bar, resulting in a high-quality coat.

Curing and cooling
Curing is done at 225o C, post which water sprays are used for cooling.
TECHNICAL
Standard
Parameter | ASTM 775/A775 M-16 (Reaffirmed 2019) |
IS 13620: 1993 (Reaffirmed 2004) |
ET TMT EPOXY COATED BARS |
Coating Thickness | 175-400 (microns) | 100-300 (microns) | 100-300 (microns) |
Coating Holidays | 9 holidays/3m (max.) | 20 holidays/3m (max.) | 20 holidays/3m (max.) |
Coating Flexibility (Achieved) | Bend at 180 on specific mandrel at 45secon to complete | Bend at 120 on specific mandrel at 90 seconds to complete | Bend at > 120 on specific mandrel at 60 seconds to complete |
Resistance to Applied Voltage/CD Test | |||
Abrasion Resistance | Max. 100 mg/1000 cycle | Max. 100 mg/1000 cycle | Max. 100 mg/1000 cycle |
Knoop Hardness | - | Min. 16 HK | Min. 20 HK |
Concrete Bonding Strength | Min. 85 % | Min. 80 % | Min. 90 % |
TECHNICAL
Standard
Coating Thickness
175-400 (microns)
Coating Holidays
9 holidays/3m (max.)
Coating Flexibility (Achieved)
Bend at 180 on specific mandrel at 45secon to complete
Resistance to Applied Voltage/CD Test
Abrasion Resistance
Max. 100 mg/1000 cycle
Knoop Hardness
–
Concrete Bonding Strength
Min. 85 %
Coating Thickness
100-300 (microns)
Coating Holidays
20 holidays/3m (max.)
Coating Flexibility (Achieved)
Bend at 120 on specific mandrel at 90 seconds to complete
Resistance to Applied Voltage/CD Test
Abrasion Resistance
Max. 100 mg/1000 cycle
Knoop Hardness
Min. 16 HK
Concrete Bonding Strength
Min. 80 %
Coating Thickness
100-300 (microns)
Coating Holidays
9 holidays/3m (max.)
Coating Flexibility (Achieved)
Bend at > 120 on specific mandrel at 60 seconds to complete
Resistance to Applied Voltage/CD Test
Abrasion Resistance
Max. 100 mg/1000 cycle
Knoop Hardness
Min. 20 HK
Concrete Bonding Strength
Min. 90 %
Laboratory Testing
Onsite Testing
Laboratory Testing
A series of critical tests are carried out as per standards to confirm the coat quality.
Chemical Resistance Test
Bars are immersed in solutions per BIS 13620:1993 norms to test chemical resistance.
Adhesion of Coating
Bars are bent to 120o around a mandrel in 60 seconds to test the adhesion of the coating. This is done as per BIS 13620: 1993 norms.
Abrasion Test
The resistance of the coating on coated panels to abrasion is tested by a Taber Abraser as per the procedure mentioned in BIS 13620:1993.
Salt Spray Resistance
Exposure to salt sprays is done as per ASTM-775 recommendations to test resistance to wet and corrosive environments.
Resistance to an Applied Voltage
The effect of electrical and electrochemical stresses on the bond and integrity of the coating is assessed as per BIS 13620:1993.
Impact Test
Mechanical damage resistance is tested with the falling weight test as per BIS 13620: 1993.
Onsite Testing
ET Epoxy-Coated TMT bars undergo several laboratory and onsite testing experiments for performance assessments.
The coastal area in Mandapam, Rameshwaram is considered to have the world’s second most corrosive environment. The comparative performance results of ET Epoxy-Coated Bars with CRS TMT Bars and Bare TMT Bars are presented here.
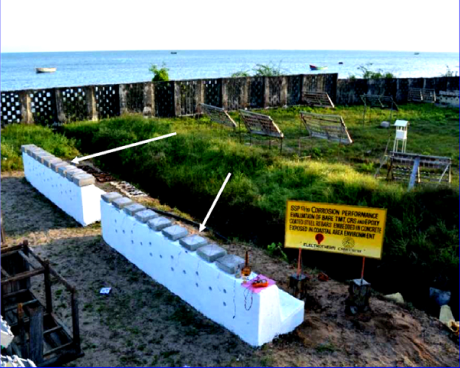
Mandapam, Rameshwaram Seashore
Laboratory Testing
Onsite Testing
A series of critical tests are carried out as per standards to confirm the coat quality.
Chemical Resistance Test
Bars are immersed in solutions per BIS 13620:1993 norms to test chemical resistance.
Adhesion of Coating
Bars are bent to 120o around a mandrel in 60 seconds to test the adhesion of the coating. This is done as per BIS 13620: 1993 norms.
Abrasion Test
The resistance of the coating on coated panels to abrasion is tested by a Taber Abraser as per the procedure mentioned in BIS 13620:1993.
Salt Spray Resistance
Exposure to salt sprays is done as per ASTM-775 recommendations to test resistance to wet and corrosive environments.
Resistance to an Applied Voltage
The effect of electrical and electrochemical stresses on the bond and integrity of the coating is assessed as per BIS 13620:1993.
Impact Test
Mechanical damage resistance is tested with the falling weight test as per BIS 13620: 1993.
Laboratory Testing
Onsite Testing
ET Epoxy-Coated TMT bars undergo several laboratory and onsite testing experiments for performance assessments.
The coastal area in Mandapam, Rameshwaram is considered to have the world’s second most corrosive environment. The comparative performance results of ET Epoxy-Coated Bars with CRS TMT Bars and Bare TMT Bars are presented here.
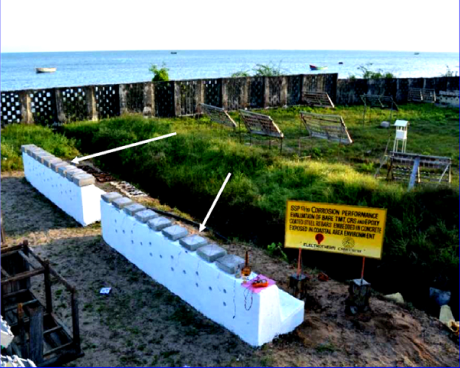
Mandapam, Rameshwaram Seashore
EPOXY-COATED TMT BAR PERFORMANCE BEHAVIOUR
Corrosion Testing in Laboratory Under Simulated Conditions
Laboratory simulation for coastal, salty and humid conditions.
A 5% NaCl solution was sprayed for 48 days by creating a humid ambient as per ASTM 775 standard. 6 mm holes were drilled on epoxy coated bars.
Observation: No cracking/fatigue/
coating disbondment visible nearby the drilled holes in coated bars, while the bare bar was completely corroded.
coating disbondment visible nearby the drilled holes in coated bars, while the bare bar was completely corroded.
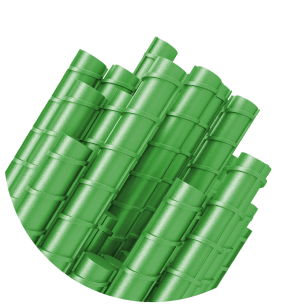
Epoxy Coated TMT
Bare TMT
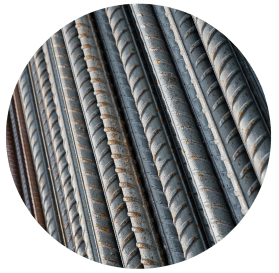
PRE-FABRICATED CUT & BEND ET EPOXY COATED TMT BARS
Advantages
1
Automatic Italian Schnell machines ensure cutting and bending efficiency,
accuracy, and uniformity.
2
High force resistance and ductility. Ductility enables cutting and bending sans
wear and tear.
3
Perfect joints with closed-loop reinforcement for lateral support. Provide shear
reinforcement in beams.
4
Available in superior finish in all desired angles and shapes in CNC bars, refined
steel bars, and superior steel bars.
5
Closed loop reinforcement for lateral support provides shear reinforcement
in beams.
6
The customer pays only for the theoretical blueprint weight. Saves on freight and
on cumbersome handling and wastage in onsite cutting and bending.
7
Best suited for critical design structures such as windmills, flyovers, bridges, etc.
enhance the structure’s life
Application
Epoxy-Coated TMT Bars are used in heavy structures and cantilever structures in corrosive environments. They play a critical role in strengthening concrete subjected to corrosive
exposure such as deicing salts and marine environments.
Coastal Areas
Bridge & Flyover
Dams
Sea Water
APPROVED BY
Government Agencies
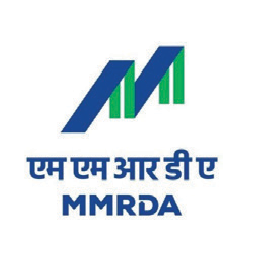
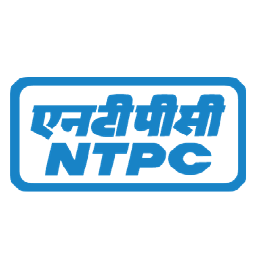
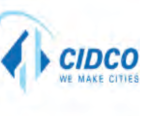
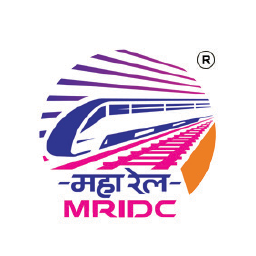
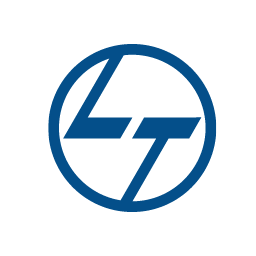
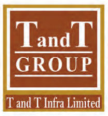
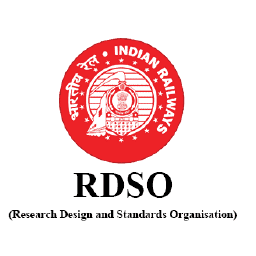
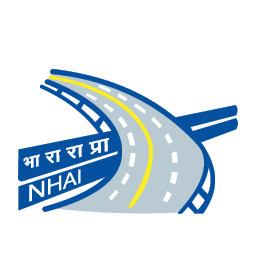
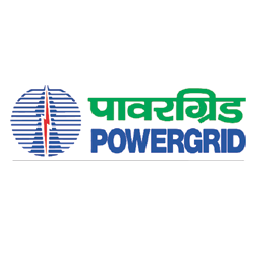
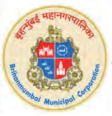
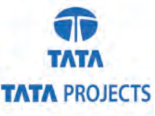
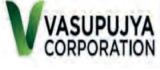
From the blog