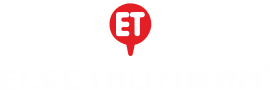
A Trusted Name for
Over Four Decades
40
Years
71
Counteries
6000
Installation
AN

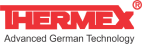



certified company.
Electrotherm India is Western Bharat's
leading steel manufacturing company and
a world leader in induction melting
furnaces.
Electrotherm India is Western Bharat's leading steel manufacturing company and a world leader in induction melting furnaces.
ET TMT, a part of the Electrotherm Group, is
Western Bharat’s first fully integrated facility for
manufacture of TMT bars.
ET TMT, a part of the Electrotherm Group, is Western Bharat’s first fully integrated facility for manufacture of TMT bars.
Electrotherm India, founded in Gujarat, Bharat, in 1983, is a well-diversified holding company with a
strong presence in steel & pipe manufacturing, steel
plant equipment, transformers, TMT bars, battery-
operated electric vehicles, renewable energy,
transmission line towers, and education.
We have a strong global presence in continuous
casting machines and ladle refining furnaces.
Electrotherm India, founded in Gujarat, Bharat, in 1983, is a well-diversified holding company with a strong presence in steel & pipe manufacturing, steel plant equipment, transformers, TMT bars, battery-operated electric vehicles, renewable energy, transmission line towers, and education.
We have a strong global presence in continuous casting machines and ladle refining furnaces.
ET TMT
ET TMT
A FOUNDATION OF
INNOVATIONS
A FOUNDATION OF
INNOVATIONS
Innovation at Work
Innovation
at Work
In keeping with the ever-rising quality expectations of our customers and our long history of innovations,
we at ET TMT endeavour to raise our standards through constant innovations to enhance process
efficiency and product quality.
In keeping with the ever-rising quality expectations of our customers and our long history of innovations, we at ET TMT endeavour to raise our standards through constant innovations to enhance process efficiency and product quality.
ELdFOSTM Patented Technology
The ELdFOSTM metallurgic process is an ET TMT patented technology. It is used for enhanced
dephosphorization in ladle and desulphurization in the
ladle refining furnace for steel. This process can bring
down sulphur & phosphorus levels to 0.02 % each in
the steel. This refines steel as per BIS.
The ELdFOSTM metallurgic process is an ET TMT patented technology. It is used for enhanced dephosphorization in ladle and desulphurization in the ladle refining furnace for steel. This process can bring down sulphur & phosphorus levels to 0.02 % each in the steel. This refines steel as per BIS.
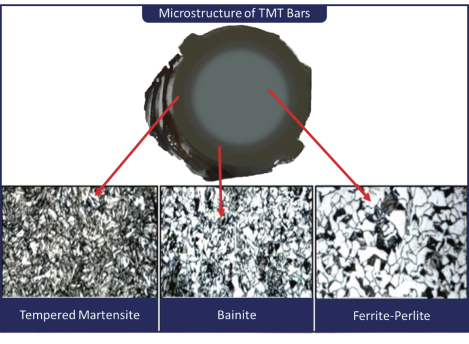
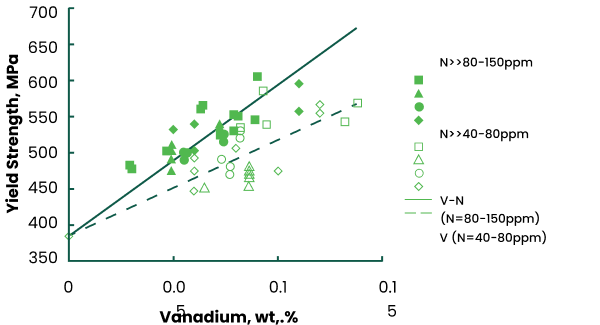
Innovative Vanadium
Micro-Alloyed Steel
Vanadium micro-alloyed steel, an ET TMT invention, has high ductility over a wide temperature range and is
less prone to cracking during continuous casting &
bending of rebar. Adding of 0.1% Vanadium results in
savings of 10% to 15% on steel consumption and carbon
footprint reduction.
With relatively high ductility over a wide temperature range, vanadium steel is also less prone to cracking during continuous casting at lower reheat temperatures.
Vanadium is distributed uniformly during rolling, resulting in low rolling loads.
With relatively high ductility over a wide temperature range, vanadium steel is also less prone to cracking during continuous casting at lower reheat temperatures.
Vanadium is distributed uniformly during rolling, resulting in low rolling loads.
This steel has high ductility over a wide temperature range and is less prone to cracking during continuous casting & bending of rebar. Addition of 0.1% Vanadium results in savings of 10% to 15% on steel consumption and reduction of carbon footprint.
Relatively high ductility over a wide temperature range, vanadium steel is less prone to cracking during continuous casting at lower reheat temperature as well.
Vanadium is distributed uniformly during rolling resulting in low rolling loads.
Relatively high ductility over a wide temperature range, vanadium steel is less prone to cracking during continuous casting at lower reheat temperature as well.
Vanadium is distributed uniformly during rolling resulting in low rolling loads.
Innovative Vanadium
Micro-Alloyed Steel
This steel has high ductility over a wide temperature
range and is less prone to cracking during continuous
casting & bending of rebar. Addition of 0.1% Vanadium
results in savings of 10% to 15% on steel consumption
and reduction of carbon footprint.
Relatively high ductility over a wide temperature
range, vanadium steel is less prone to cracking during
continuous casting at lower reheat temperature as
well.
Vanadium is distributed uniformly during rolling
resulting in low rolling loads.
range and is less prone to cracking during continuous
casting & bending of rebar. Addition of 0.1% Vanadium
results in savings of 10% to 15% on steel consumption
and reduction of carbon footprint.
Relatively high ductility over a wide temperature
range, vanadium steel is less prone to cracking during
continuous casting at lower reheat temperature as
well.
Vanadium is distributed uniformly during rolling
resulting in low rolling loads.
This steel has high ductility over a wide temperature range and is less prone to cracking during continuous casting & bending of rebar. Addition of 0.1% Vanadium results in savings of 10% to 15% on steel consumption and reduction of carbon footprint.
Relatively high ductility over a wide temperature range, vanadium steel is less prone to cracking during continuous casting at lower reheat temperature as well.
Vanadium is distributed uniformly during rolling resulting in low rolling loads.
Relatively high ductility over a wide temperature range, vanadium steel is less prone to cracking during continuous casting at lower reheat temperature as well.
Vanadium is distributed uniformly during rolling resulting in low rolling loads.
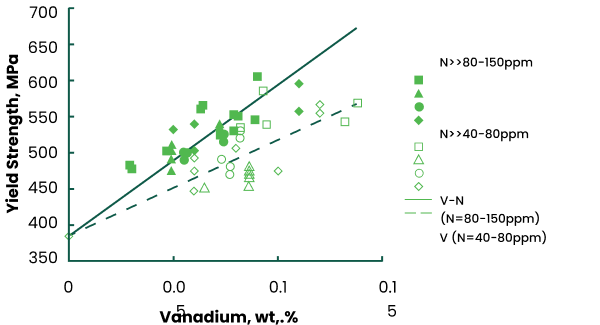
Recognition
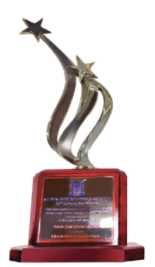
2019, 2022
The Ispat Agradoot Awards
Government of Bharat
ET TMT was awarded the prestigious Ispat Agradoot Award in 2019 & 2022.
Pioneering work in integrated Iron Ore-IF-LAF route to produce high-quality ET TMT
Fe 500, Fe 500 D, Fe 550 & Fe 600 Bars won us the Ispat Agradoot Award in 2019.
Ispat Agradoot Award 2022 was given in recognition of pioneering work in steel by using integrated BF + DRI → IF → LRF → CCM (EMS) → RM → ECP route to produce high-quality Fe 500D TMT Bars. This route ensures less contamination in terms of tramp elements such as Copper, Zinc, Tin, Chromium, Nickel, Titanium etc., resulting in superior control over the chemical, mechanical & metallurgical properties of finished products in a wide range of steel grades as per varying applications.
Ispat Agradoot Award 2022 was given in recognition of pioneering work in steel by using integrated BF + DRI → IF → LRF → CCM (EMS) → RM → ECP route to produce high-quality Fe 500D TMT Bars. This route ensures less contamination in terms of tramp elements such as Copper, Zinc, Tin, Chromium, Nickel, Titanium etc., resulting in superior control over the chemical, mechanical & metallurgical properties of finished products in a wide range of steel grades as per varying applications.
ET TMT was awarded the prestigious Ispat Agradoot Award in 2019 & 2022. Pioneering work in integrated Iron Ore-IF-LAF route to produce high-quality ET TMT Fe 500, Fe 500 D, Fe 550 & Fe 600 Bars won us the Ispat Agradoot Award in 2019.
Ispat Agradoot Award 2022 was given in recognition of pioneering work in steel by using integrated BF + DRI → IF → LRF → CCM (EMS) → RM → ECP route to produce high-quality Fe 500D TMT Bars. This route ensures less contamination in terms of tramp elements such as Copper, Zinc, Tin, Chromium, Nickel, Titanium etc., resulting in superior control over the chemical, mechanical & metallurgical properties of finished products in a wide range of steel grades as per varying applications.
Ispat Agradoot Award 2022 was given in recognition of pioneering work in steel by using integrated BF + DRI → IF → LRF → CCM (EMS) → RM → ECP route to produce high-quality Fe 500D TMT Bars. This route ensures less contamination in terms of tramp elements such as Copper, Zinc, Tin, Chromium, Nickel, Titanium etc., resulting in superior control over the chemical, mechanical & metallurgical properties of finished products in a wide range of steel grades as per varying applications.
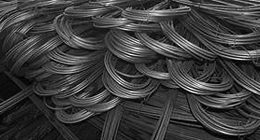
How to choose the right TMT
bar for your structure?
How to choose the right TMT bar for your structure?
Have Questions? Call us Now
Sales: +91 8238079223
Need Support? Write to us
salestmt@electrotherm.com